New moulds and products
We will support you in part and mould design before mould making and start of production
-
We recommend using flow simulation to support part design
-
Flow simulation will confirm manufacturability of a product and helps to eliminate problems and risks well i advance
-
When needed we can use pressure and temperature sensors to get data directly out of the mould cavity.
We will support in selecting the right sized moulding machine for your product
-
Correct clamping force
- Correct volume flow (right screw diameter and injection unit)
-
Correct residence time for the raw material
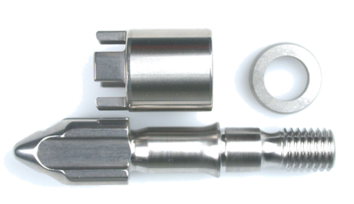
Ramping up new tools and getting tools approved at tool makers is our expertise. We will trim the moulds based on the quality requirements from the customer and we document the process before transfering moulds to production facility. Naturally we will support ramping up production at the factory.
- Mould trials and trimming can be done at the mould maker or at the moulder.
- Before production mould acceptance, mold and part quality will be assured to comply with the requirements and specifications of the customer.
- Moulds will always be delivered to moulding facility tested and documented
- The first production run can be used as a final approval and the achieved moulding process will be analyzed for yield, cycle time and robustness.
Are you interested in our services. Please feel free to contact us!
References
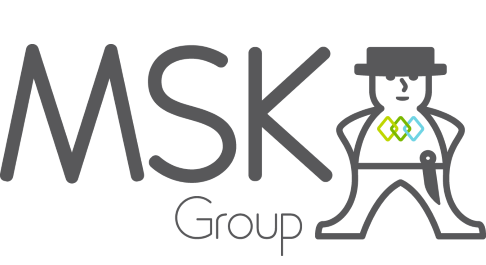

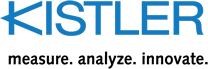

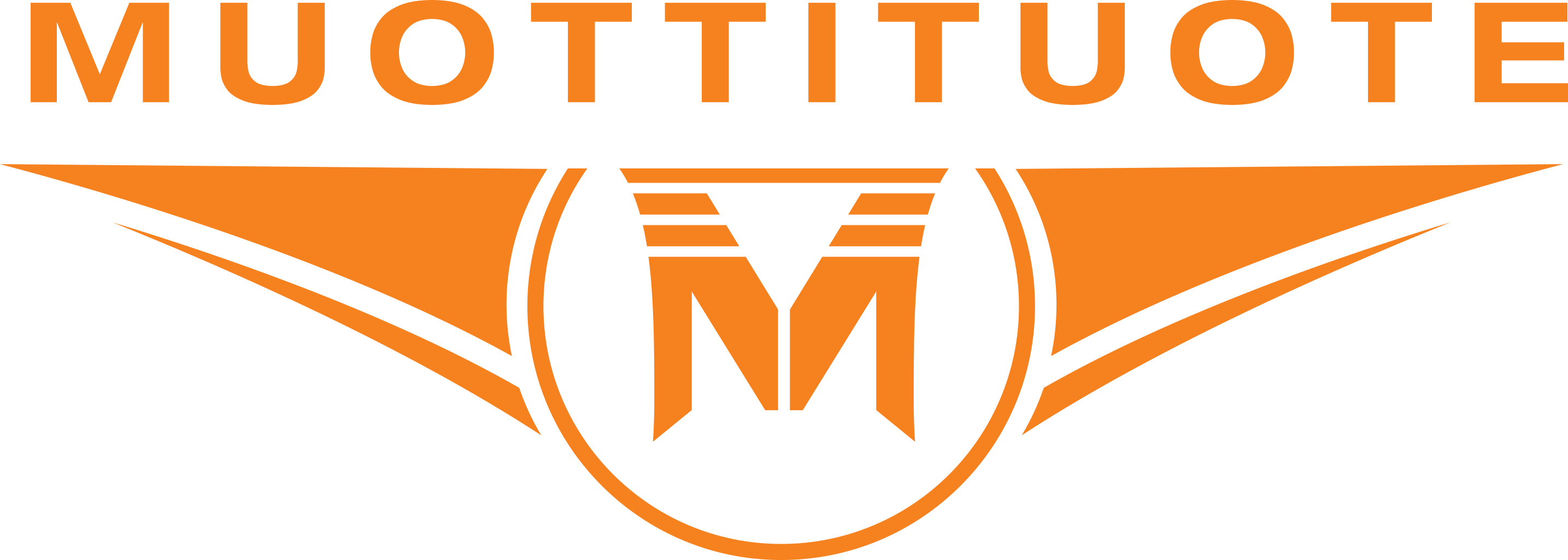